Principi di funzionamento delle macchine utensili
Breve disamina sulle caratteristiche principali di un fresatore CAD-CAM
Introduzione
La prima idea di macchina comandata da un programma di lavoro precompilato e il conseguente prototipo iniziale è storia recente risalendo agli anni attorno al 1950, ma in questo breve periodo di tempo si è assistito auna rapida e intensa evoluzione che ha interessato e coinvolto tutti i settori della produzione industriale, fino a toccare il settore dentale,
prima con i servizi offerti da grossi centri di produzione, arrivando poi anche a creare un’offerta di prodotti adottabili direttamente dai laboratori odontotecnici.
Una così repentina disponibilità e diffusione di prodotti e servizi non è però stata accompagnata da una necessaria informazione e formazione allo scopo di preparare gli utenti finali di questa rivoluzione che hanno accolto il cambiamento alcuni con diffidenza e scetticismo, non sapendo cogliere i vantaggi che questa tecnologia offriva, altri con slancio e determinazione,
diventando i pionieri di un nuovo corso, con tutti i vantaggi e gli svantaggi dell’essere i precursori del cambiamento.
La possibilità di ritrovare opinioni molto contrastanti negli utilizzatori rende chiaro come sia necessario avvicinare questi sistemi con conoscenza e competenza per evitare che un’opportunità si trasformi in una fonte di frustrazione.
Scopo di questo articolo è cercare di fornire alcune informazioni di base indispensabili per comprendere al meglio il funzionamento di una macchina utensile, in modo da poter interagire più consapevolmente con le proposte che l’attuale tecnologia disponibile sul mercato mette a disposizione.
Concetti di base sulle lavorazioni utensili
Uno dei primi concetti da introdurre, se non il più importante, è quello che sta alla base del funzionamento delle macchine di produzione (principalmente torni e macchine fresatrici) tramite asportazione di materiale, che partono cioè da un blocco di materiale più o meno grezzo e, tramite opportuni movimenti programmati e l’uso di utensili specifici, rimuovono il materiale in eccesso andando a restituire il pezzo lavorato nella sua forma definitiva: il materiale deve poter essere adeguatamente formato attraverso opportune lavorazioni di taglio o abrasione.
Questo dipende principalmente dalle caratteristiche meccaniche intrinseche del materiale che faranno cadere la scelta sul tipo di lavorazione più idoneo e conseguentemente sui relativi utensili.
Non tutti i materiali infatti sono in grado di essere lavorati attraverso operazioni di taglio, ma a causa della loro fragilità e della scarsa deformabilità plastica richiedono di essere sottoposti ad abrasione: il materiale grezzo viene messo a contatto con un materiale generalmente più duro secondo la scala di Mohs e questo per attrito asporta dalla superficie delle particelle generando al tempo stesso una notevole quantità di calore.
Si tratta di un’operazione poco efficiente in quanto la maggior parte dell’energia cinetica applicata viene dispersa in calore e la quantità di materiale rimosso è molto limitata, richiedendo di conseguenza un gran numero di ripetizioni del movimento di lavorazione.
Oltre a questo bisogna considerare il fatto che l’energia liberata sotto forma di calore deve essere velocemente asportata dall’interfaccia tra materiale e abrasivo attraverso un opportuno fluido lubrificante, in quanto un aumento incontrollato della temperatura potrebbe portare all’insorgere di cricche o fratture nel materiale grezzo e un rapido decadimento del materiale abrasivo per compromissione del legante, ma al tempo stesso il fluido lubrificante ridurrà ulteriormente la già minima efficienza della lavorazione.
A fronte di questi inconvenienti che rendono molto dispendiosa in termini di tempo questa lavorazione, bisogna considerare che la superficie del pezzo lavorato sarà estremamente levigata e rifinita.
È la lavorazione con cui vengono affrontati i materiali ceramici (vetroceramica, disilicato di litio) e imateriali che contengono al loro interno materiale riempitivo inerte (compositi o resine con fibra di vetro), oppure i materiali metallici nel caso di lavorazioni particolari quali rettifiche o lappature per portare il pezzo entro rigidi parametri di tolleranza o di rugosità superficiale.
Una lavorazione più efficiente e anche più diffusa è quella di taglio che può essere applicata su materiali che presentino un grado di deformabilità da medio a elevato, per esempio cere, resine non caricate o metalli, in quanto durante l’azione di taglio dell’utensile avviene un fenomeno di asportazione di materiale similare a quello di un cucchiaino che affonda in una vasca di gelato: la parte tagliente dell’utensile si avvicina al materiale; al primo contatto, il materiale inizia a offrire una certa resistenza, ma al proseguire della spinta subisce una deformazione plastica che lo fa deformare e scorrere lungo la parete del tagliente distaccandosi dal resto del grezzo (Fig. 1), con la formazione di una scaglia o di un ricciolo detti truciolo.
Quello che si nota è che la temperatura della zona di deformazione è superiore a quella dovuta al solo attrito e le caratteristiche meccaniche della parte rimossa sono qualitativamente differenti dal materiale grezzo iniziale.
È quindi chiaro come in questo caso lo scopo del fluido lubrificante non è tanto di raffreddare l’interfaccia di taglio tra materiale e utensile, cosa per altro non sempre desiderata in quanto alcuni materiali richiedono una temperatura di lavoro abbastanza alta per rendere la zona più plastica e quindi lavorabile, cosa altrimenti difficilmente realizzabile, ma principalmente per facilitare la rimozione del truciolo ed evitare che questo possa attaccarsi alle lame del tagliente oppure al materiale residuo, potendo causare danni anche piuttosto seri se dovessero essere saturati o parzialmente ostruiti, tanto da rendere inefficaci i canali di scarico.
Se infatti analizziamo la forma generica di un utensile da taglio (Fig. 2) notiamo un gambo, generalmente liscio, che serve per la solidarizzazione diretta o indiretta al mandrino rotante della macchina, una zona di raccordo rastremata e un’elica con pendenza più o meno ripida che finisce in una punta a profilo cilindrico o sferico.
Il produttore dell’utensile progetta lo strumento sulla base di come deve essere realizzato il taglio e del profilo che deve essere impresso sul materiale grezzo, ma solo la parte iniziale è lavorante, in grado di asportare truciolo; anche se questa prosegue con una struttura a elica, generalmente serve esclusivamente ad allontanare i detriti di lavoro dalla superficie del grezzo.
Risulta chiaro quanto sia fondamentale rispettare i parametri di utilizzo indicati dal produttore degli utensili, verificati in fase di progetto e collaudo dal costruttore della macchina, perché anche l’utensile più bello o più costoso presente sul mercato potrebbe essere reso inefficace da una strategia di lavoro poco curata oppure dovendo richiedere alla macchina prestazioni che non è in grado di erogare perché fuori dai propri parametri di progetto.
La quantità di materiale asportato dal tagliente durante l’approccio al grezzo deve essere perfettamente calibrata per rendere efficiente il taglio: un suo eccesso potrebbe portare a un rapido accorciamento della vita dell’utensile che si tradurrebbe in uno scarso numero di ore di lavoro affrontabili o numero di pezzi prodotti, mentre una sua eccessiva riduzione potrebbe generare fenomeni di incollamento del truciolo o di tagliente di riporto, con superfici irregolari e poco rifinite, fino a situazioni limite in cui per uno scarso affondamento il tagliente invece di mordere il grezzo e creare delle scaglie tenderebbe a scivolare al di sopra, strisciando sulla superficie e generando per attrito una notevole quantità di calore, sufficiente in materiali delicati come il titanio a superare la temperatura di 880° in cui avviene un cambiamento dello stato cristallino e si genera un indurimento della superficie in grado addirittura di consumare il materiale di cui è realizzato l’utensile e distruggerlo.
Un’ulteriore categoria di materiali frequentemente utilizzati in campo dentale è rappresentata dall’ossido di zirconio presinterizzato e affini.
Questa tipologia di materiale ha un comportamento simile a entrambi i tipi finora affrontati, ma allo stesso tempo molto differente.
Infatti, nel suo stato finale di sinterizzazione può essere lavorato, ma con molta difficoltà, solo attraverso abrasione, mentre nel suo stato di presinterizzazione con cui viene normalmente fornito non subisce un vero e proprio effetto di taglio perché è privo della capacità di deformazione plastica alle temperature di utilizzo; è più simile, volendo mantenere un esempio di tipo alimentare, a un cucchiaino che affonda in un blocco di zucchero.
Le deboli forze che legano assieme i grani vengono rotte e portano al modellamento del grezzo, ma devono essere utilizzati utensili specifici in quanto si tratta di un materiale estremamente duro e abrasivo e per questo le lame dei taglienti vengono rivestite di uno strato di diamante per limitare il loro consumo e prolungarne la vita utile, oltre a dover resistere alle temperature che si sviluppano nella zona di taglio per l’attrito generato; non è raro vedere zone rosse incandescenti utilizzando strumenti di scarsa qualità o portati oltre il limite di ore di lavoro.
Da questa breve e semplificata disamina di ciò che avviene durante la lavorazione di un materiale grezzo per costruire un semilavorato tramite asportazione di materiale si nota chiaramente come alcune situazioni richiedano caratteristiche tecniche che sono in contrapposizione tra di loro: materiali duri e fragili necessitano di macchine delicate, veloci e con mandrini con alte o altissime velocità di rotazione, mentre materiali resistenti ma malleabili preferiscono basse velocità di rotazione, alte forze di spinta e soprattutto strutture portanti estremamente robuste in grado di sopportare il carico di lavoro.
Analizzeremo quindi ora, sempre in maniera semplificata, le principali sezioni con cui è costruita una macchina fresatrice, offrendo le necessarie informazioni per passare da semplici spettatori del balletto che gli utensili compiono attorno al grezzo per realizzare il pezzo finito a coreografi del proprio spettacolo.
Fig.1_ Microfotografia di una lavorazione di taglio su metallo.
La parte scura a destra rappresenta lo
strumento che sta affondando nel materiale.
Si nota nella parte verticale il truciolo che si deforma e si stacca
seguendo il profilo del tagliente.
All’interno del truciolo è evidente la struttura deformata secondo piani
paralleli che si compatta secondo da direzione di taglio.
Fig.2 Piccolo campionario di utensili rotanti e non e relativi accessori di
montaggio. Ogni lavorazione richiede specifiche soluzioni per ottenere il
risultato voluto in modo efficiente.
I componenti strutturali di una macchina fresatrice
Abbiamo finora analizzato cosa avviene all’internodi una macchina fresatrice durante il processo di lavorazione.
Andiamo ora a esaminare da quali componenti è formata, a cosa servono e come questi possono influenzare i risultati delle lavorazioni.
Sinteticamente ogni macchina fresatrice è costituita da un elettromandrino rotante su cui vengono montati, manualmente o in automatico, gli utensili; un sistema di bloccaggio del materiale grezzo da lavorare; un complesso sistema di movimentazione del grezzo, della testa lavorante o di entrambi, che può comprendere meccanismi per eseguire spostamenti lineari e rotazioni attorno ad uno o più assi, a seconda della complessità della macchina e dei pezzi da lavorare; un sistema elettronico di coordinamento delle azioni, il controllo numerico, che deve interpretare ed eseguire il programma di lavoro elaborato dall’operatore, manualmente o tramite un apposito software CAM che avendo in memoriale caratteristiche specifiche della macchina, le informazioni sul materiale e la forma dettagliata del pezzo da realizzare elabora la sequenza di movimenti necessari a liberare l’oggetto desiderato dal materiale in eccesso che lo intrappola.
«Ogni blocco di pietra ha una statua dentro di sé ed è compito dello scultore scoprirla» –Michelangelo.
Dell’elettromandrino abbiamo già in parte descritto il funzionamento parlando dei vari tipi di utensili.
Occorre però ribadire che come esistono moltissime tipologie di utensili, con caratteristiche differenti di funzionamento, esistono altrettanti tipi di elettromandrino che si differenziano fondamentalmente per la velocità di rotazione che riescono a raggiungere e per la coppia sviluppata, cioè la forza che viene erogata durante la rotazione.
È piuttosto evidente che per affrontare il taglio di materiali metallici, magari utilizzando utensili di diametro importante, è necessario un elettromandrino con una coppia molto elevata soprattutto a bassi giri, altrimenti potrebbe andare in stallo non riuscendo ad asportare il materiale.
Viene generalmente consigliato dai produttori di utensili di affrontare la lavorazione di metalli con una velocità di rotazione tra i 4000 e i 10000 rpm, mentre pe rlavorazioni abrasive di ceramica o similari si consiglia di partire da almeno 30000 fino a 50000rpm o oltre.
Non tutte le macchine utensili sono in grado di soddisfare una gamma di esigenze così ampia, ma la cosa importante, qualunque tipo di elettromandrino si decida di adottare, è di prestare particolare attenzione al sistema di raffreddamento impiegato per disperdere il calore prodotto durante la lavorazione.
Sia la rotazione che la spinta assiale e verticale, per quanto supportate da ottimi cuscinetti, generano comunque una notevole quantità di calore all’interno dell’elettromandrino che se non correttamente gestita può introdurre dannose deformazioni termiche che causano un lavoro non corretto dei cuscinetti, generando rotazioni eccentriche e vibrazioni che possono causare scarsa qualità della superficie del pezzo o anche un’insufficiente precisione dimensionale, oltre a danneggiare nel tempo in modo irreparabile l’elettromandrino stesso.
Gli elettromandrini di qualità superiore presentano al loro interno un sistema a circuito chiuso in cui scorre un fluido refrigerante, esattamente come avviene nei motori automobilistici: dopo aver rimosso il calore, esso viene dirottato verso uno scambiatore termico per mantenere la temperatura sempre entro livelli controllati.
L’assenza di questo accessorio deve essere presa seriamente in considerazione qualora si valuti di sottoporre la macchina a un carico di lavoro medio o elevato, magari effettuando lavorazioni notturne non sorvegliate, perché potrebbe portare a una vita decisamente breve dell’elettromandrino, con conseguenti alti costi di manutenzione non programmata e frequenti fermi macchina, danneggiandola produttività della stessa.
Un’ultima caratteristica importante dell’elettromandrino che offre un enorme vantaggio in termini di flessibilità operativa è il modo con cui viene montato e solidarizzato l’utensile.
Le versioni più datate ed economiche prevedono che l’operatore CAM provveda personalmente tramite apposite chiavi a sbloccare il mandrino, rimuovere l’utensile, posizionare il successivo e serrare nuovamente il sistema di bloccaggio.
Questo metodo richiede che l’operatore sia costantemente presente durante tutto il ciclo di fresaggio per provvedere alla sostituzione degli utensili, ma dato che i tempi di lavoro si allungano e i costi di produzione salgono velocemente, questa soluzione è stata praticamente abbandonata da tutti i produttori.
Una prima soluzione alternativa, poco vantaggiosa dal punto di vista economico, è di creare una macchina multi mandrino, in modo da ridurre l’impegno dell’operatore a dover semplicemente sostituire gli utensili usurati o danneggiati, ma la soluzione più efficiente e anche più diffusa è che l’elettromandrino possa autonomamente provvedere alla sostituzione dell’utensile in modo automatizzato.
Per realizzare ciò viene sfruttato un meccanismo a pinza: durante lo stato di riposo una molla spinge contro la pinza in modo da chiuderla e serrare l’utensile; quando è necessario procedere alla sostituzione viene applicata una forza contraria alla spinta della molla, generalmente attraverso un pistone ad aria compressa, la pinza si apre e libera l’utensile.
Questo tipo di soluzione è generalmente a dottato da mandrini di bassa potenza, in quanto la pinza non riesce a generare una grande forza di serraggio e gli utensili montabili sono un set limitato che ha in comune il diametro del gambo che deve corrispondere con il diametro della pinza.
I mandrini più versatili non si collegano direttamente all’utensile, ma attraverso un accessorio di montaggio chiamato cono (Fig. 3).
Questo supporto presenta nella parte posteriore una forma caratteristica, generalmente conica, a bassissima tolleranza che ha lo scopo di collegarsi all’elettromandrino in modo molto preciso e stabile e ha la funzione di accoppiamento e trasmissione del moto. I coni più raffinati presentano una ripetibilità di accoppiamento inferiore al micrometro.
Nella parte anteriore invece è presente il sistema di serraggio dell’utensile, che può essere composto da una pinza sostituibile e quindi adattabile a moltissimi diametri utensile, oppure a calettamento, dove con uno strumento a induzione elettromagnetica viene espansa termicamente la zona di collegamento in modo controllato e raffreddandosi blocca l’utensile in posizione; in entrambi i casi viene lasciata la libertà all’operatore di poter adottare qualunque modello di qualunque produttore di utensili senza vincoli di sorta, con una forza di serraggio che può superare anche il valore di diverse tonnellate, cosa che dà garanzia di affidabilità nelle lavorazioni più gravose, ma allo stesso tempo assicura una percentuale minima di eccentricità dell’utensile durante la rotazione.
Il secondo aspetto analizzato è relativo al sistema di bloccaggio del pezzo.
La situazione nel campo dentale è molto differente da quella dell’industria, in cui gli staffaggi sono di tipo innumerevole perché ogni pezzo grezzo è differente e talvolta il bloccaggio viene realizzato su misura; in campo dentale invece si lavora esclusivamente con grezzi pre-lavorati che vengono prodotti e distribuiti secondo standard conosciuti e rispettati, che permettono un montaggio in macchina semplice e veloce.
Ciononostante, soprattutto quando si lavorano materiali delicati e fragili, sarebbe preferibile poter utilizzare un sistema di fissaggio stabile ed esteso, in modo da evitare di avere parti del grezzo sospese che potrebbero risentire delle vibrazioni dovute alla lavorazione generando dannose crepe.
Su alcune macchine è anche possibile riscontrare la presenza di un sistema automatico di sostituzione del materiale da lavorare, con il vantaggio quindi di poter aggiungere in coda diverse lavorazioni che vengono successivamente eseguite con la possibilità di ridurre i tempi morti e poter sfruttare anche le ore notturne per massimizzare la produttività della macchina.
Possono essere realizzati tramite complessi bracci antropomorfi o anche con sistemi più semplici, ma sono generalmente riservati a realtà medio-grandi con alti volumi di produzione e cicli ininterrotti diurni e notturni.
L’argomento che riguarda la movimentazione e gli organi meccanici che la rendono possibile è sicuramente il più interessante, ma anche il più complesso e richiederebbe uno spazio decisamente superiore rispetto a quello che potremo dedicare: cercheremo di essere sintetici, ma allo stesso tempo di fornire informazioni chiare che potranno in seguito essere approfondite da chi vorrà dedicarsi all’argomento; ci scusiamo in anticipo se non potremo analizzare in dettaglio tutte le possibili varianti costruttive che i progettisti hanno adottato, ma vedremo esclusivamente le più diffuse con i loro pro e contro.
Il concetto alla base è che per realizzare un pezzo ci deve essere un movimento di avvicinamento tra il grezzo e l’utensile affinché quest’ultimo possa rimuovere il materiale in eccesso, ma si tratta di un movimento relativo: non è tanto importante che sia il grezzo a spostarsi, oppure l’utensile, quanto il fatto che il movimento sia affidabile e ripetibile.
Requisito fondamentale, alla base sia della produzione dentale che di quella industriale ingenerale, è che il pezzo prodotto sia il più vicino possibile al progetto iniziale in termini di forma e di dimensioni nelle tre direzioni dello spazio.
Una differenza importante è che mentre nell’industria esiste sempre una scheda di approvazione in cui sono specificate chiaramente dal progettista le variazioni di tolleranza entro cui il pezzo deve rientrare per essere giudicato accettabile, pena il fatto di scartare l’intero lotto di produzione, troppo spesso nel campo dentale la validazione del lavoro è fatta con parametri poco oggettivi e quantificabili, lasciando la valutazione a impressioni soggettive che poco hanno a che fare con il concetto di precisione.
Un ulteriore fatto che rende difficile il lavoro dell’operatore CAM in campo dentale è che la stragrande maggioranza delle lavorazioni, se non tutte, viene eseguita un’unica volta e deve produrre un risultato accettabile senza alcuna prova di produzione, delegando questo aspetto esclusivamente all’esperienza dell’operatore CAM.
In industria invece viene obbligatoriamente realizzata una pre-serie, misurata accuratamente, confrontata con il progetto originale in modo da correggere la lavorazione e ottimizzare il risultato in termini di qualità realizzativa e richiesta temporale per l’esecuzione.
Il concetto di precisione risulta quindi essere l’idea trainante che guida il produttore durante la progettazione della macchina e la prima richiesta dell’acquirente quando si accosta al prodotto, ma è un concetto fuorviante, deve essere correttamente compreso.
Definiamo precisione la distanza che esiste tra la misura del pezzo che viene realizzato e quella che dovrebbe invece essere la dimensione reale e quindi tanto più preciso quanto questa differenza è minima.
Se però consideriamo un oggetto che avesse una discrepanza rispetto al progetto del 3% in eccesso su un lato e del3% in difetto su un altro lato, questo comporterebbe una grossa differenza di forma nonostante la ridotta discrepanza dimensionale, ma soprattutto avrebbe come conseguenza che i pezzi prodotti sarebbero impossibili da migliorare.
Se invece si riuscisse a ottenere la stessa identica discrepanza su entrambi i lati, fosse anche questa di entità decisamente maggiore, per ipotesi il 30% (10 volte di più), saremmo in una condizione decisamente migliore perché potremmo facilmente agire sul sistema di taratura e regolazione del movimento per portare la discrepanza prossima allo zero.
Ecco che quindi il concetto di precisione deve essere supportato e reso inseparabile da quello di ripetibilità, perché in sua assenza ci si potrebbe esclusivamente affidare al caso e sperare che il prodotto finito si avvicini a quello progettato.
Come si può quindi ottenere una precisione ripetibile all’interno di una macchina utensile?
Fondamentalmente utilizzando una struttura rigida e poco sensibile alle deformazioni termiche, applicando sistemi di controllo delle movimentazioni lineari e rotative e gestendo il grado di eccentricità di rotazione degli utensili.
Una struttura rigida e indeformabile è tanto più importante quanto più elevati sono gli sforzi messi in atto per lavorare materiali resistenti come i metalli.
I vari produttori utilizzano generalmente alluminio, per contenere il peso complessivo della macchina e facilitarne trasporto e installazione, oppure diversi di tipi di acciaio per garantire maggiore robustezza e affidabilità nel tempo.
Alcuni produttori hanno scelto di realizzare le basi di assemblaggio delle proprie macchine in un’unica struttura di ghisa realizzata in un monoblocco di diverse tonnellate, riservandole ad ambienti opportuni e dedicati a causa della complessità e dei requisiti di installazione, mentre altri hanno scelto di realizzare la struttura portante in granito naturale o sintetico, andando a copiare le caratteristiche di resistenza, affidabilità e precisione tipici dei banchi di misura utilizzati in metrologia, dove la necessità di fornire misure affidabili e costanti nel tempo è un requisito imprescindibile.
Oltre a questo il granito, attraverso la sua non omogeneità interna dovuta alla struttura granulare, offre il vantaggio di ridurre la trasmissione delle vibrazioni e di evitare fenomeni di risonanza, migliorando quindi la finitura superficiale e riducendo la rumorosità prodotta durante le lavorazioni.
Alla struttura di supporto viene quindi fissato il sistema di movimentazione, costituito generalmente da una o più guide per ogni asse su cui scorre un pattino, vincolato secondo un’unica direzione e mosso attraverso un motore che a seconda della rotazione oraria o antioraria esegue un’azione di trascinamento o spinta.
Nel corso degli anni sono stati messi a punto sistemi molto raffinati per ridurre al minimo gli attriti e i giochi tra i vari componenti, tanto che le macchine utensili attuali utilizzano viti e guide a ricircolo di sfere (Figg. 4-6), in modo che i componenti in movimento non si tocchino direttamente, ma attraverso l’interposizione di un canale in cui scorrono delle sfere di acciaio o ceramica per trasformare l’attrito da radente a volvente, permettere un elevato precarico in modo da azzerare i giochi di inversione di movimento e vincolare saldamente i movimenti lungo un unico asse.
L’efficienza di questi sistemi e la loro semplicità di implementazione sono ormai così assodati che le macchine che non fanno ricorso a questa classe di accessori dovrebbero essere tranquillamente scartate senza alcun ripensamento.
A queste finezze progettuali può essere aggiunto ancora un gruppo di accessori che permette di fare un salto di qualità enorme perché purtroppo i componenti meccanici, anche di ottima qualità realizzativa e assemblati nel modo più scrupoloso, tendono a usurarsi con il tempo e quindi a perdere l’affidabilità che possedevano al momento della prima installazione.
Viene quindi in soccorso uno strumento di misura chiamato encoder o riga ottica, che interfacciandosi direttamente con il controllo numerico controlla costantemente, diverse migliaia di volte al secondo, che la posizione raggiunta da un movimento di traslazione lineare o di rotazione di un asse sia quello richiesto dal programma di lavoro; qualora questo fosse diverso provvede a informare il controllo numerico che in modo completamente automatico e senza l’intervento dell’operatore corregge la posizione fino a raggiungere la quota necessaria, garantendo una più accurata e ripetibile lavorazione.
Tutti gli organi meccanici, come le viti senza fine e le chiocciole, sono soggetti a usura meccanica con il passare del tempo, ma anche durante lavorazioni molto impegnative possono essere colpite da deformazioni termiche non omogenee nelle zone a più alto sforzo (Fig. 7): il sistema di misura tramite riga ottica rileva la posizione reale della tavola e la confronta con quella teorica, decidendo automaticamente di quanto correggere il movimento e compensando quindi l’errore in tempo reale, cosa impossibile da realizzare anche da un operatore molto esperto.
È dimostrato che in appena 20 minuti di lavoro una vite a ricircolo di sfere, con il solo calore dovuto all’attrito del movimento, presenta una dilatazione di 0,1mm/m, cosa inaccettabile se si considera che una semplice connessione implantare a esagono interno viene resa inutilizzabile quando presenta una discrepanza dimensionale di +/- 0,005 mm; senza uno strumento di verifica in tempo reale, tale dilatazione non potrà essere gestita né controllata, causando una deformazione dimensionale del manufatto (Figg. 8, 9).
Un ultimo aspetto da tenere in considerazione per cercare di ottenere la tanto agognata precisione è relativo alla dimensione degli utensili impiegati nella lavorazione.
Ogni produttore fornisce classi diverse dello stesso tipo di utensili a seconda che questi siano utilizzati per operazioni di sgrossatura o di finitura, dichiarando anche le tolleranze di produzione, ma durante l’assemblaggio dell’utensile al mandrino si potrebbero introdurre dei difetti di posizione rendendo l’utensile non perfettamente coassiale rispetto all’assedi rotazione, generando quindi un aumento del diametro fittizio di lavorazione, con una maggiore asportazione di materiale e una conseguente imprecisione finale del pezzo.
L’elettromandrino inoltre, a causa di collisioni avvenute durante la sua vita oppure per un decadimento delle caratteristiche dei cuscinetti, potrebbe aver variato il suo grado di eccentricità di rotazione, migliorabile esclusivamente con la sua sostituzione o con una importante e costosa manutenzione realizzata presso il produttore.
Per questi motivi le macchine più raffinate utilizzano un sistema di misura diametro che all’inizio di ogni lavorazione verifica in modo automatico l’utensile in rotazione e comunica il valore al controllo numerico che provvede automaticamente a modificare il programma di lavoro per adeguarlo al diametro corretto.
Va da sé che la correzione non deve superare limiti chiari e prestabiliti perché altrimenti comprometterebbe la vita dell’utensile portando a una rapida usura delle parti taglienti dovuta a una lavorazione non ortogonale, ma può anche indicare un errore di montaggio dell’utensile per un inaccurato controllo da parte dell’operatore, prevenendo quindi danni difficilmente rimediabili in lavorazioni che impiegano diverse ore per essere portate a termine.
Ultimo tassello che compone una macchina utensile, ma non per ordine d’importanza, è il controllo numerico, il cuore elettronico che controlla e armonizza i movimenti, più volte citato durante la disamina degli altri componenti.
Risulta chiaro da quanto detto in precedenza quanto importante sia e quale mole di dati debba elaborare in tempo reale in modo da garantire un lavoro di alta qualità.
Per questo motivo deve essere selezionato trai modelli professionali e non tra i prodotti di hobbistica, come talvolta si trova su macchine di fascia più bassa per contenere i costi di produzione ,perché la sua funzione durante lo svolgimento di un programma di lavoro elaborato da un software CAM non è passiva, di sola lettura ed esecuzione del movimento, ma bensì attiva, intervenendo a migliorare l’esecuzione, rendendola fluida e precisa.
I controlli numerici professionali contengono infatti al loro interno algoritmi che analizzano il percorso di lavoro prima dell’inizio della lavorazione, in modo da validare il movimento secondo le caratteristiche intrinseche della macchina, segnalando all’operatore eventuali errori presenti all’interno, come per esempio movimenti di traslazione o rotazione fuori dai limiti della macchina che se eseguiti porterebbero a collisioni, al danneggiamento del pezzo o dell’utensile, fino a componenti della macchina stessa.
Altre funzioni servono invece a rendere fluido il movimento e funzionano riconoscendo la traiettoria lungo la quale l’utensile deve muoversi eliminando o regolarizzando un eventuale eccesso di punti creati dal software CAM, rendendo la macchina meno “nervosa” e permettendo di ottenere superfici più rifinite.
All’opposto invece deve essere in grado di riconoscere gli spigoli, quelle zone in cui il tragitto di lavoro prevede un repentino cambio di direzione, cosa mal tollerata dalla macchina utensile che può mettere sotto sforzo motori e guide.
I controlli numerici più basilari tendono a raccordare le linee di cambio con un arco di cerchio, cosa che però comporta un’imprecisione sul pezzo finito che sarà mancante di un bordo (pensiamo per esempio agli spigoli di una connessione implantare esagonale), mentre i controlli numerici più avanzati, contenendo al loro interno i dati specifici di quella macchina, correggono il percorso senza raccordare e deformare le geometrie, ma applicando i necessari cambiamenti nella velocità di esecuzione, eventualmente rallentando prima del cambio di direzione e accelerando progressivamente subito dopo, allo stesso modo di un automobilista che dovesse affrontare una curva stretta ad alta velocità.
Un altro esempio di algoritmi interni di ottimizzazione è relativo al sistema di interpolazione delle curve.
Se immaginiamo di dover disegnare su un foglio a quadretti un cerchio annerendo in sequenza i quadretti necessari capiamo che più questi sono piccoli e numerosi, più la forma sarà rispettosa dell’idea originaria di cerchio che è quindi funzione della matrice disponibile.
Il controllo numerico deve essere in grado di riconoscere le parti di percorso di lavoro che seguono una traiettoria non rettilinea, analizzarli e confrontarli con la matrice di movimento della macchina, in modo da aggiungere i punti necessari per rendere la superficie meno spigolosa.
Oltre a questi sistemi di ottimizzazione pre-lavoro esistono anche verifiche fatte in tempo reale durante la lavorazione; come già accennato, il sistema a feed-back che controlla costantemente la posizione reale di movimenti e traslazioni e li corregge istantaneamente, ma anche controlli di sforzo dei singoli motori, che siano essi legati al momento degli assi o dell’elettromandrino stesso, per evitare sovraccarichi strutturali o deformazioni; controlli di presenza e flusso del fluido lubrificante, controlli di temperatura sull’elettromandrino o sugli azionamenti dei motori; tutte verifiche utili a proteggere la macchina e salvaguardare la sua durata nel tempo.
Fig.3_Esempio di utensili di dimensioni e caratteristiche tecniche
molto differenti montati su cono per elettromandrino con cambio
utensile automatizzato.
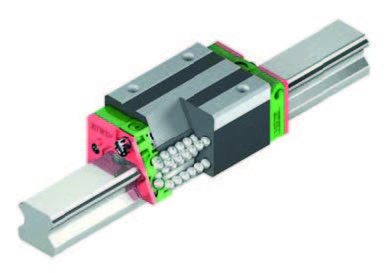 |
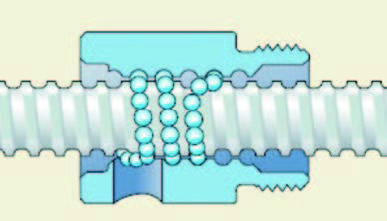 |
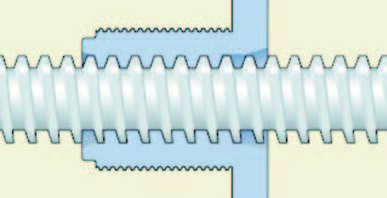 |
Fig.4 |
Fig.5 |
Fig.6 |
Figg. 4-6_Guida (Fig. 4) e vite
con chiocciola (Fig. 5), entrambe a ricircolo di sfere. In questo tipo di soluzione la parte fissa e la parte mobile non entrano in contatto direttamente come ad esempio il modello in (Fig. 6), ma scivolano su un letto di sfere che riducono l’attrito nonostante l’alto precarico permettendo di azzerare i giochi.
|
|
La versione tradizionale senza
sfere invece deve mantenere
necessariamente dello spazio che però non impedisce una lenta e costante usura, oltre a generare un’imprecisione notevole, soprattutto durante i cambi di direzione. |
Fig.7_L'immagine mostra il riscaldamento che subisce una
vite senza fine durante una serie di movimenti di traslazione. Come si
può notare la distribuzione non è omogenea: la deformazione termica
conseguente, in caso di assenza di un sistema di misura di feed-back a
riga ottica, genererà una distorsione dimensionale nel pezzo fresato non
uniforme.
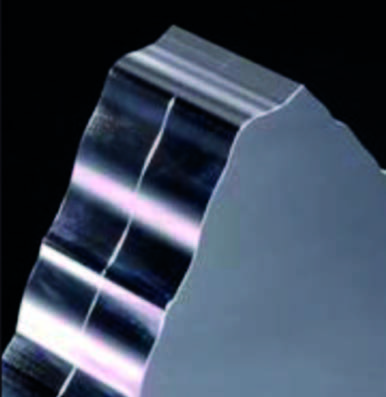 |
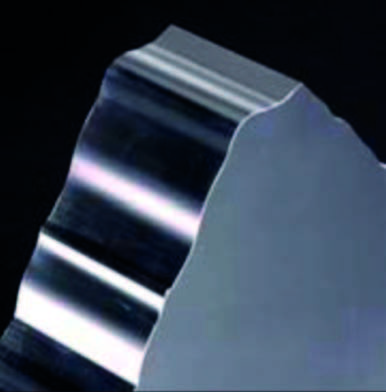 |
Fig.8 |
Fig.9 |
Effetto di una lavorazione (Fig. 8) senza controllo a feed-back della posizione tramite riga ottica.
Si può notare un gradino presente tra la prima passata di finitura e la seconda perché il sistema non è in
grado di riposizionarsi correttamente a causa dei giochi e della dilatazione termica.
La stessa lavorazione (Fig. 9) eseguita con la correzione del controllo numerico sulla base dei dati
reali di posizione consente di ottenere un qualità superficiale ottimale.
Conclusioni
Da questa breve disamina — che andrebbe ulteriormente approfondita su ognuno dei punti trattati e integrata di altri interessanti concetti collegati (per esempio dalla creazione dei percorsi di lavoro alla scelta degli utensili) — si capisce quanto sia fondamentale espandere la propria conoscenza sul funzionamento delle macchine utensili e software relativi, per poter approcciare in modo corretto la produzione di pezzi fresati tramite tecnologia CAD-CAM.
È dunque necessario acquisire informazioni mediante il confronto con colleghi esperti e, una volta individuate le proprie esigenze di lavoro, frequentare un corso teorico-pratico presso una struttura che quotidianamente produce lavorati con il CAD-CAM; il nostro consiglio, basato su un’esperienza di oltre 15 anni nel campo, è di farlo prima di iniziare la ricerca di una macchina che possa rispondere alle caratteristiche ideali per le lavorazioni che si vogliono introdurre.
In un secondo momento ci si potrà affidare agli esperti di aziende serie, in grado di proporre e produrre soluzioni adatte alle esigenze di lavoro specifiche e soprattutto capaci di accompagnare l’utente, guidandolo passo passo durante il percorso di apprendimento, in modo da poter imparare a sfruttare al massimo le potenzialità a sua disposizione.
Se si trascurano questi passaggi, il rischio concreto è di fare investimenti troppo onerosi per le proprie esigenze o al contrario di orientarsi su attrezzature più economiche, ma inadatte al tipo di lavori che si desidera produrre; in ogni caso, l’esperienza può risultare frustrante e non permettere di trarre i reali vantaggi che le lavorazioni CADCAM possono offrire se bene impostate.